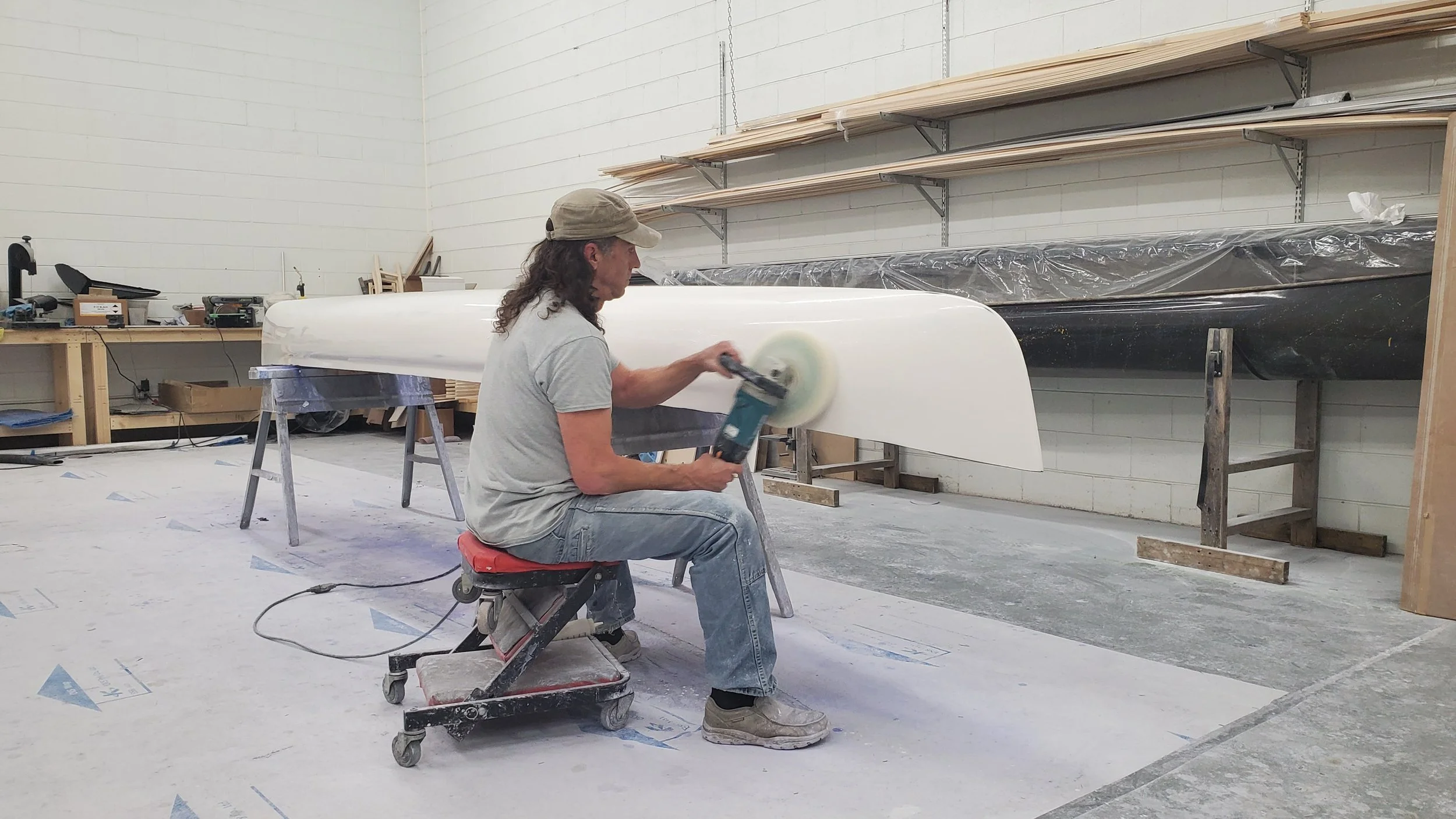
Fiberglass & Composite Repair in the Twin Cities
Specializing in Canoes, Kayaks, SUPs, Boats & More
40+ Years of Experience
Family-Owned
Quality Service
Why NORD ProShop?
NORD ProShop (NPS) is a local Twin Cities family business centered around general fiberglass repair with an emphasis on small watercraft such as canoes, kayaks, SUP, fishing/hunting boats and the like. With a combined experience of over 40 years in an array of composite professions, the NPS team is dedicated to getting you the results you need and often exceeding expectations.
If it’s made of Fiberglass, Kevlar, Carbon, or any other manner of composite material, we have you covered. For all watercraft composed of plastic or aluminum, no problem! Fill out the quote form and we will advise accordingly.
NPS works closely with our neighbors at Forever Fabrication who specializes in all metal work including aluminum canoe welding repair and boat trailer repair.
Our Services
Consultations
Sometimes all you need is a couple questions answered and some basic instruction over the phone. You can schedule a consultation with Kent directly or contact us during our normal business hours for a “walk-in”.
A minimum charge of $20.00 will be collected before the consultation begins. $1.50 per minute will be added for every minute beyond initial 20 minutes.
General Fiberglass Repair & Production
Basically, if it’s made of fiberglass, we can build it/fix it. Typical repairs include snowmobile hoods and belly pans, bathtub repair, rooftop cargo carriers, etc.
Low Volume Production & OEM - If you provide a mold, we can build a few units for you such as snowmobile parts, carbon fiber or glass car parts, custom motorcycle parts, etc.
We typically do not do Automotive or Aviation repair or production however, feel free to reach out and we will do what we can to help you find a solution.
Small Marine Repair
NPS Specializes in small watercraft repair. We pride ourselves on our ability to work with thin laminates which pose a challenge to most general repairmen. Most thin laminations will often show signs of repair, however we strive to return all watercraft to their near-original luster.
All watercrafts must be under 20’ in length. We do not work on motors.
-
Canoes/Kayaks/SUP: Kevlar, Royalex/Plastic, Fiberglass, Aluminum, Carbon Fiber, Wood Strip, Wood and Canvas
Sailboat Hulls, Rowboats, Drift Boats, Duck Boats (Layout Boat), Ice Boats
Pulk Sleds
Paddles
And more!
Tooling, Composite Molding, and Prototyping
NPS enjoys creating new molds for Composite Production or One-Off replacement parts as well as Fiberglass Art Pieces. For inquiries about molding or prototyping please call Eli directly for a quote.
DIY Classes and Professional Clinics
NPS offers informal classes on basic composite repair. We hold group classes once a month for groups of 2-8 people. We also perform off-site clinics for professional repair shops that may have lost some key talent and need some crash course training.
Classes & Clinic Scheduling: Please contact Eli directly.
If you are interested in advanced composite courses in in-mold gel coating, infusion, vacuum bagging, tooling, molding, design, etc, please contact Eli.
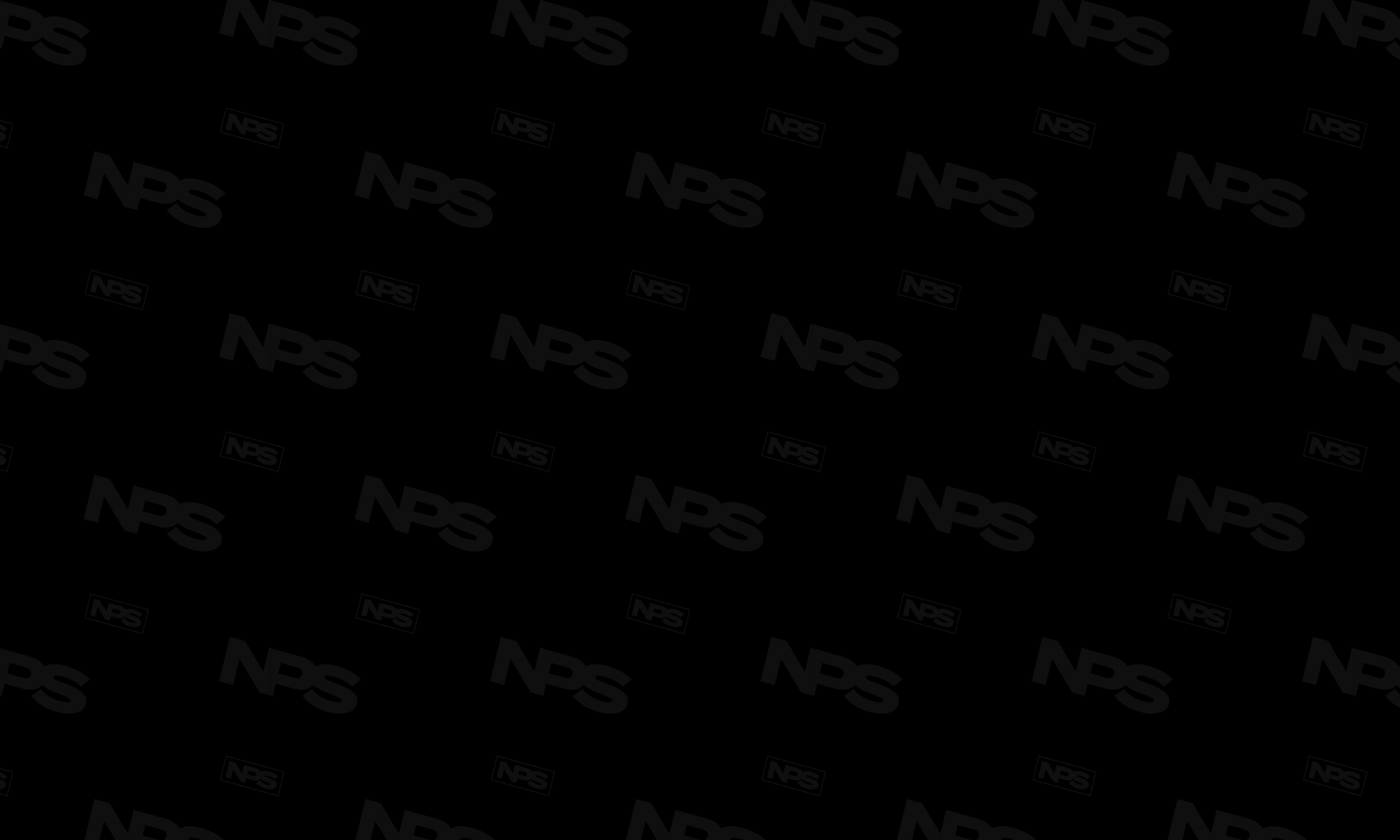
Meet the NPS Team
NPS is owned and operated by Eli Nord with the support of his recently retired Father, Kent Nord.
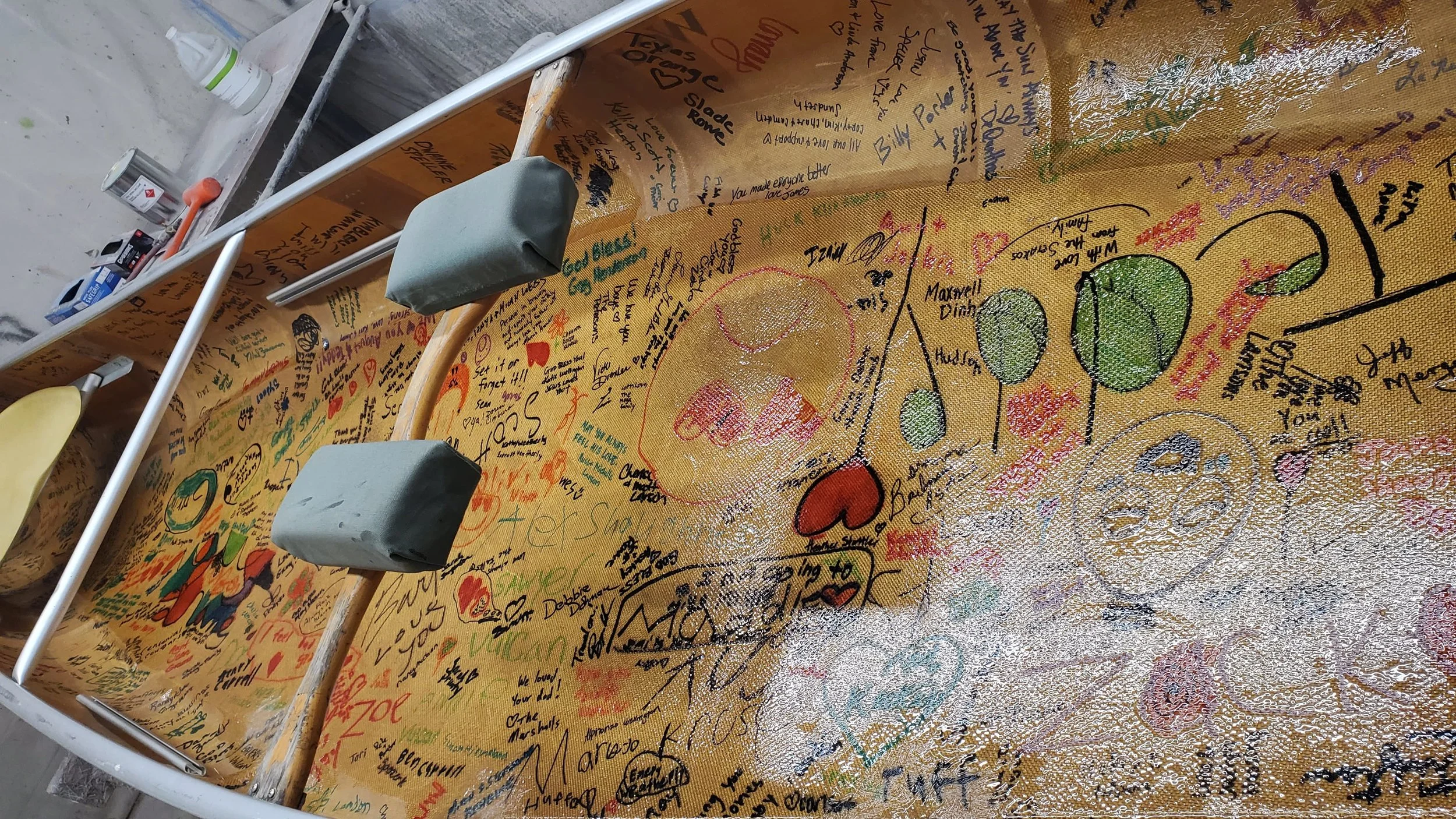
Kent Nord
With over 30 years of professional experience in the manufacturing/repair industry, Kent has worked for companies such as Bell Canoe Works as the trim shop manager, Northwest Canoe Company teaching cedar strip boat building and small watercraft repair, Grey Duck Outdoors as a canoe/mold designer, and Imperial Boat Repair as the Lead Repairman for every kind of marine vessel imaginable. There isn’t much Kent has not seen and fixed. Although he is enjoying retirement from full-time work, Kent loves new challenges and his passion for boats continues to be a light in his life.
Eli Nord
Eli has over 10 years of professional experience in the manufacturing and composite tooling industry. Eli’s specialties are centered around product development and boat design. Eli has worked with companies such as Northstar Canoes as the trim shop manager and Jr. R&D Engineer, Grey Duck Outdoor as Lead Canoe Designer/Developer, Consultant for Current Design Kayaks, Redfeather Canoes, Merrimack Canoes, Sanborn Canoe Company, and Freelance Boat Repair for several years. If you have a mold to build or a composite product to prototype, Eli is the guy to talk to.
Our Work
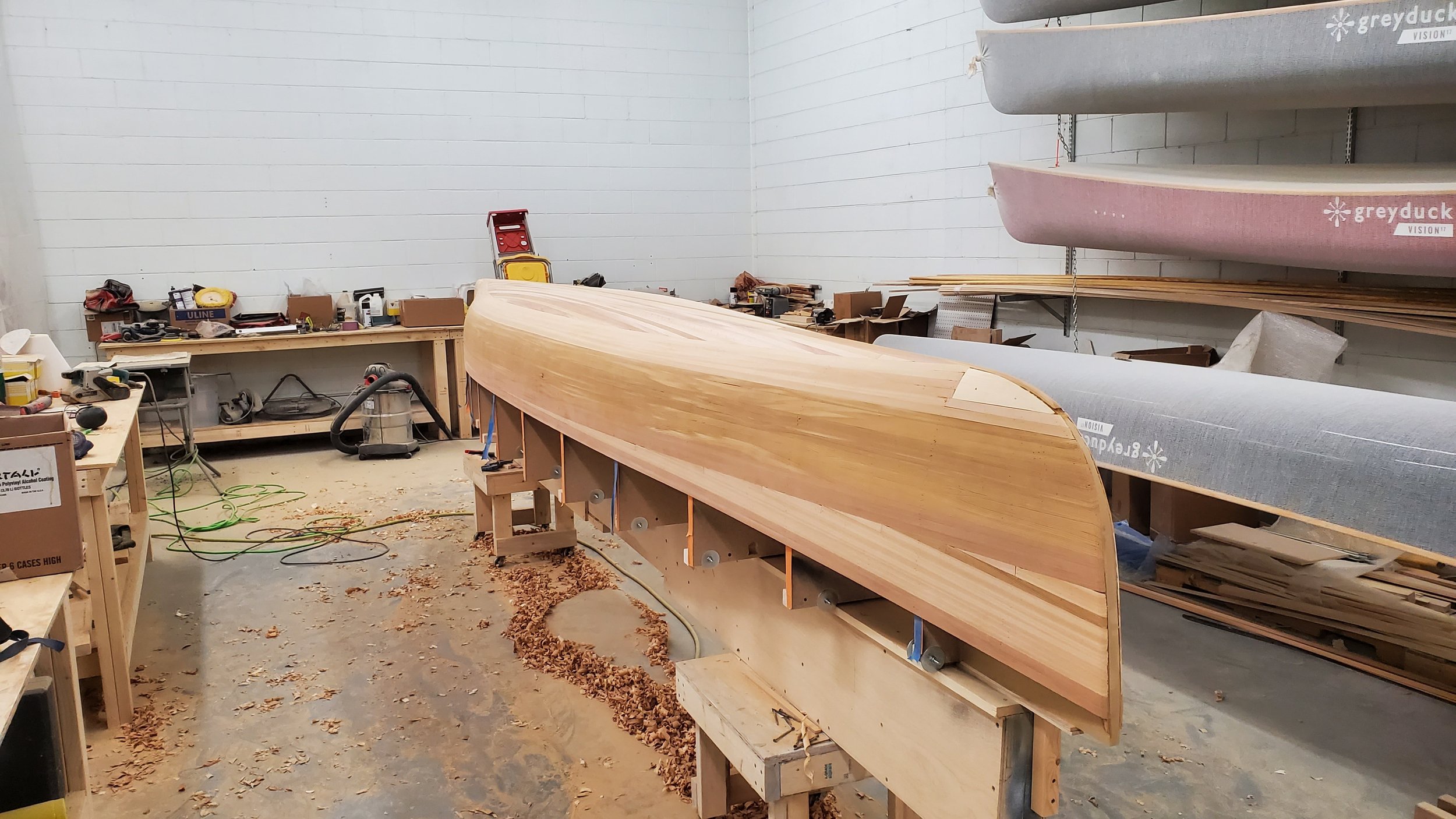
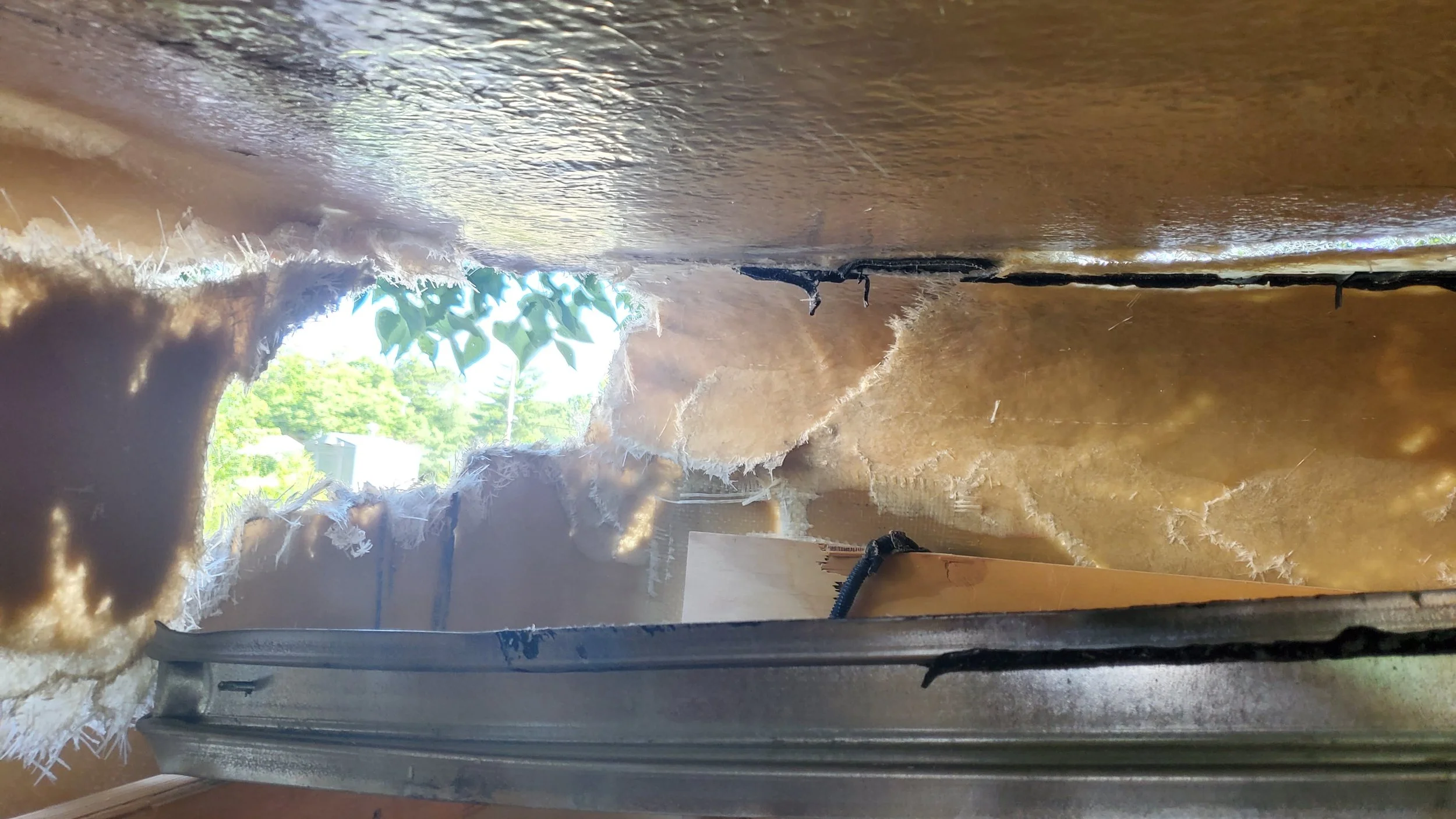
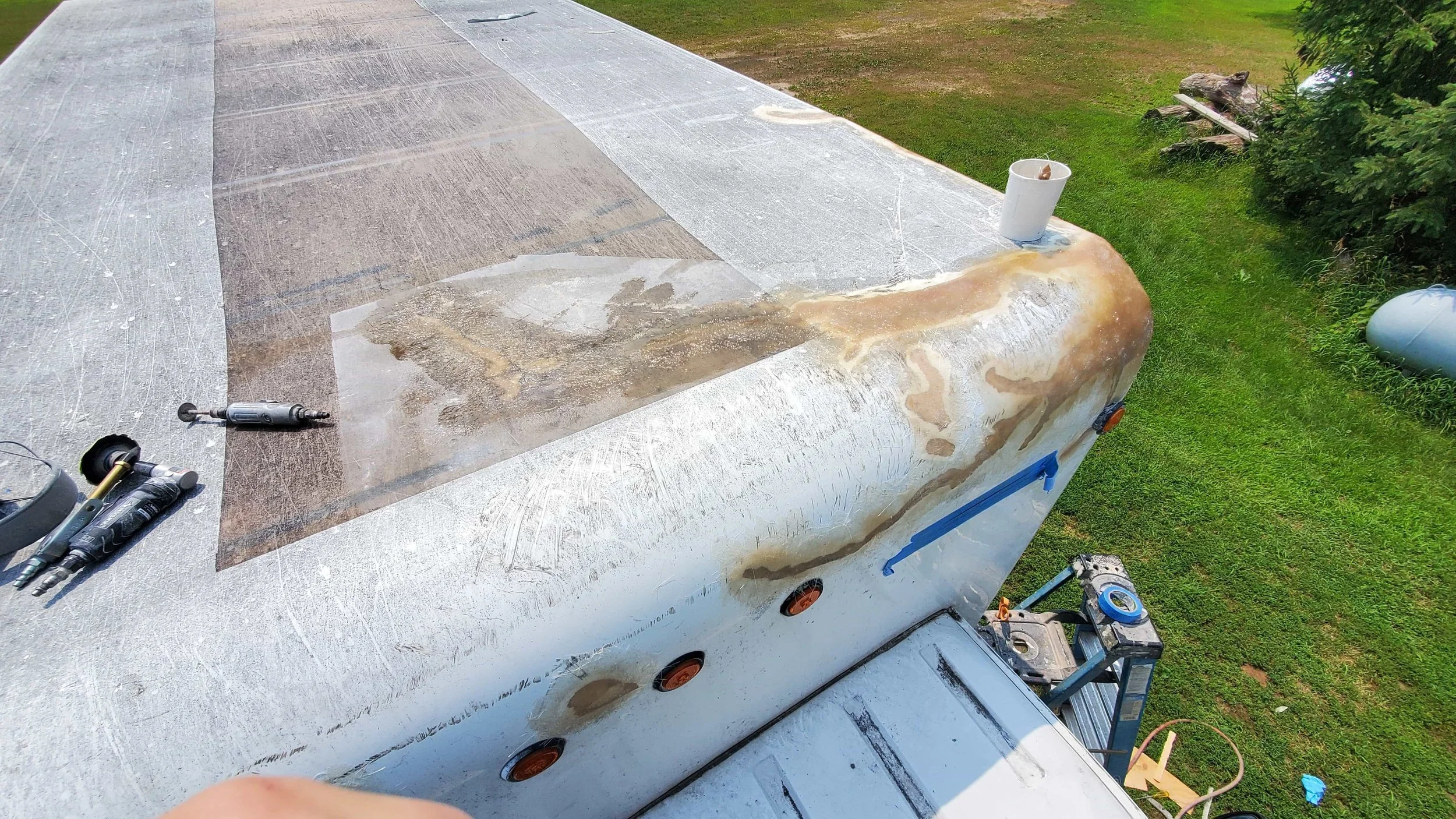
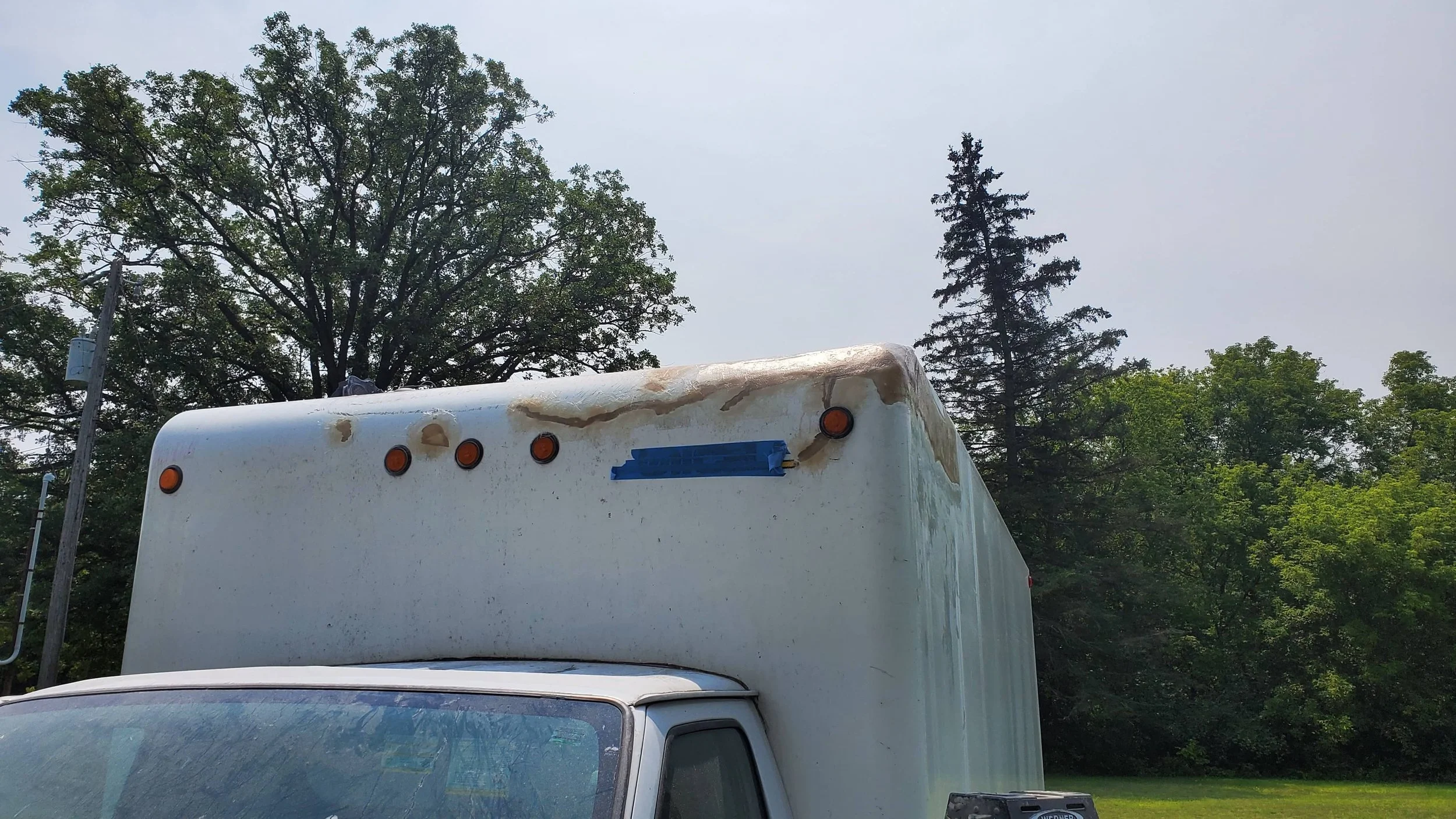
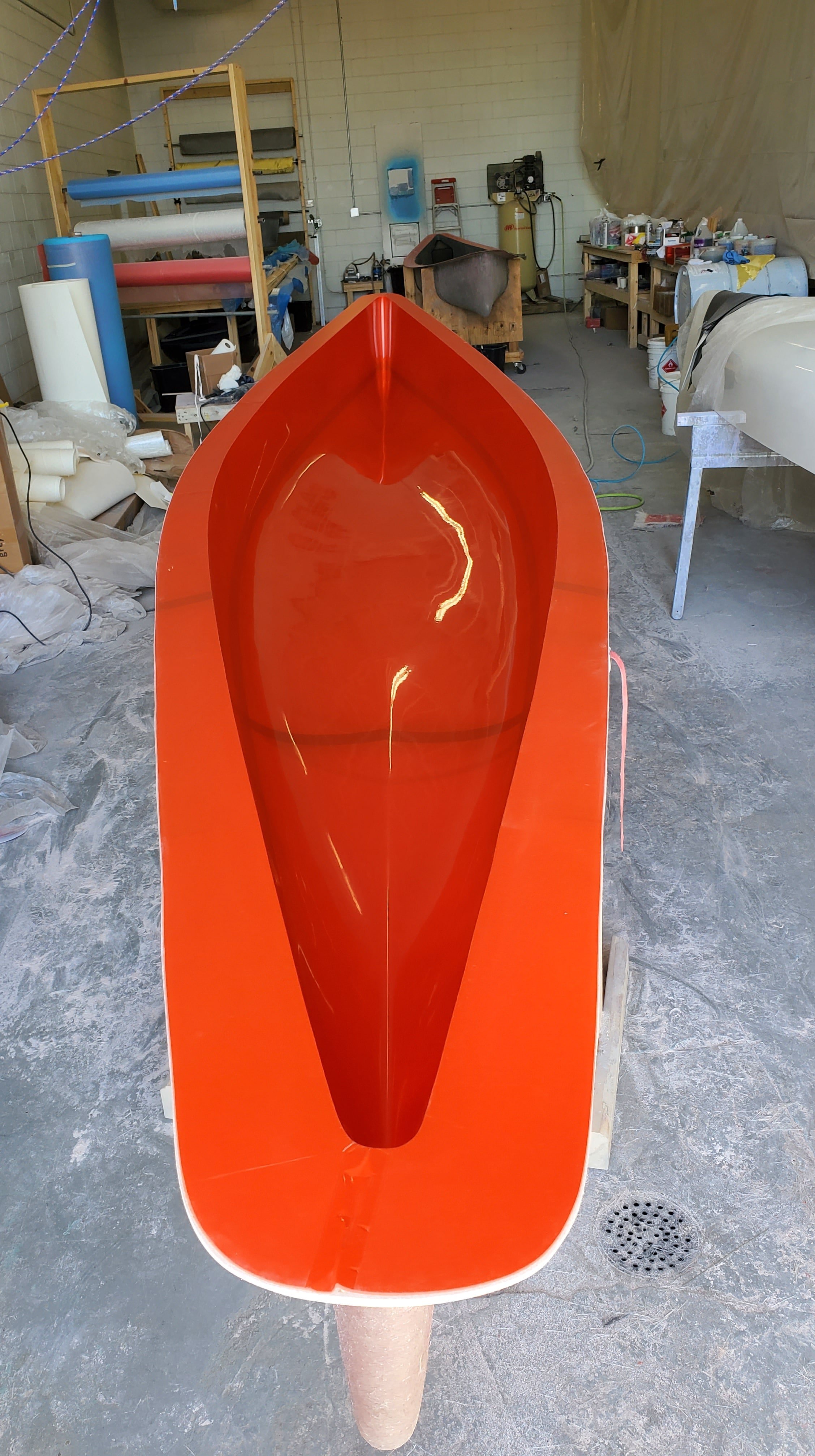


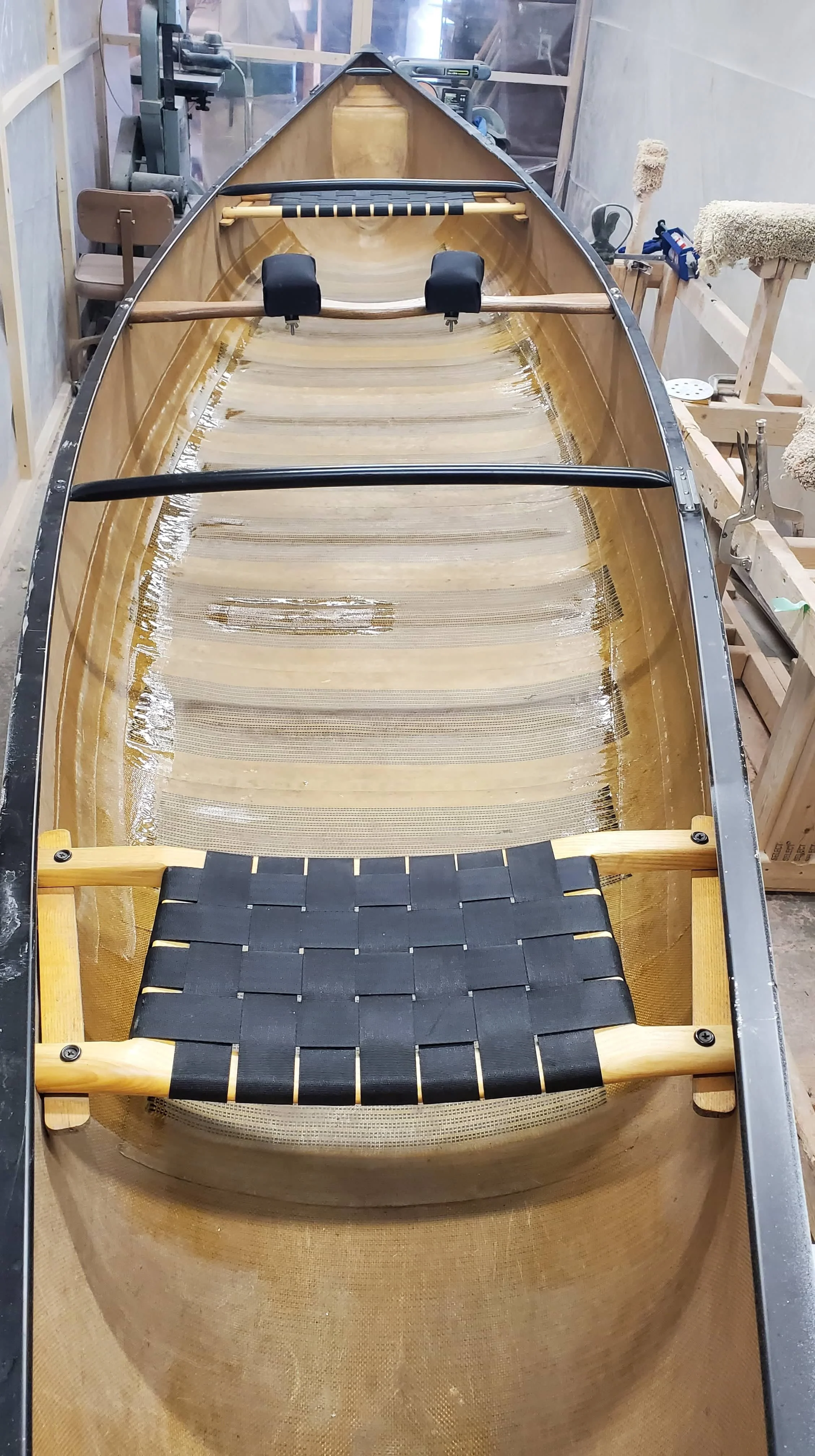


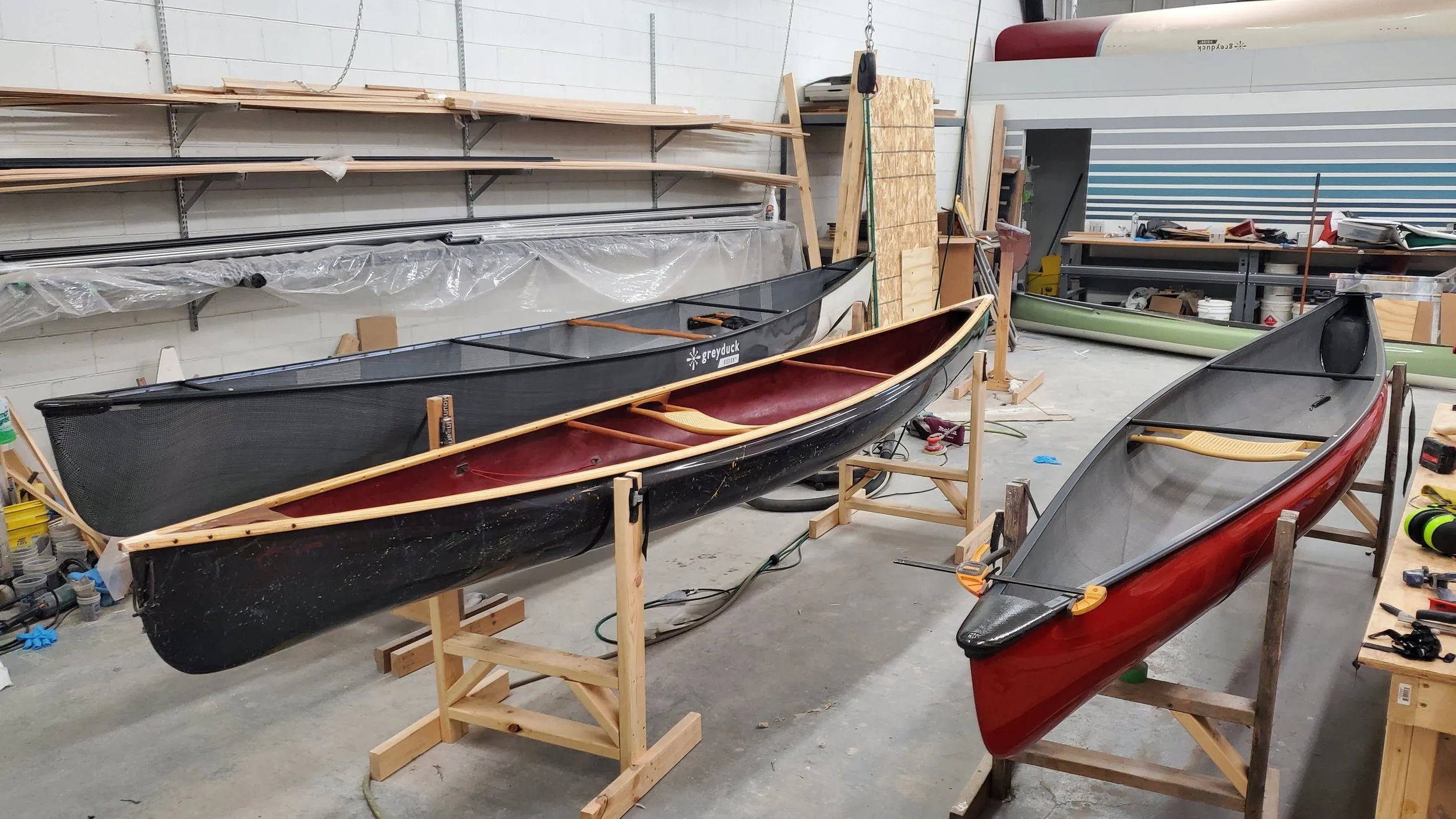
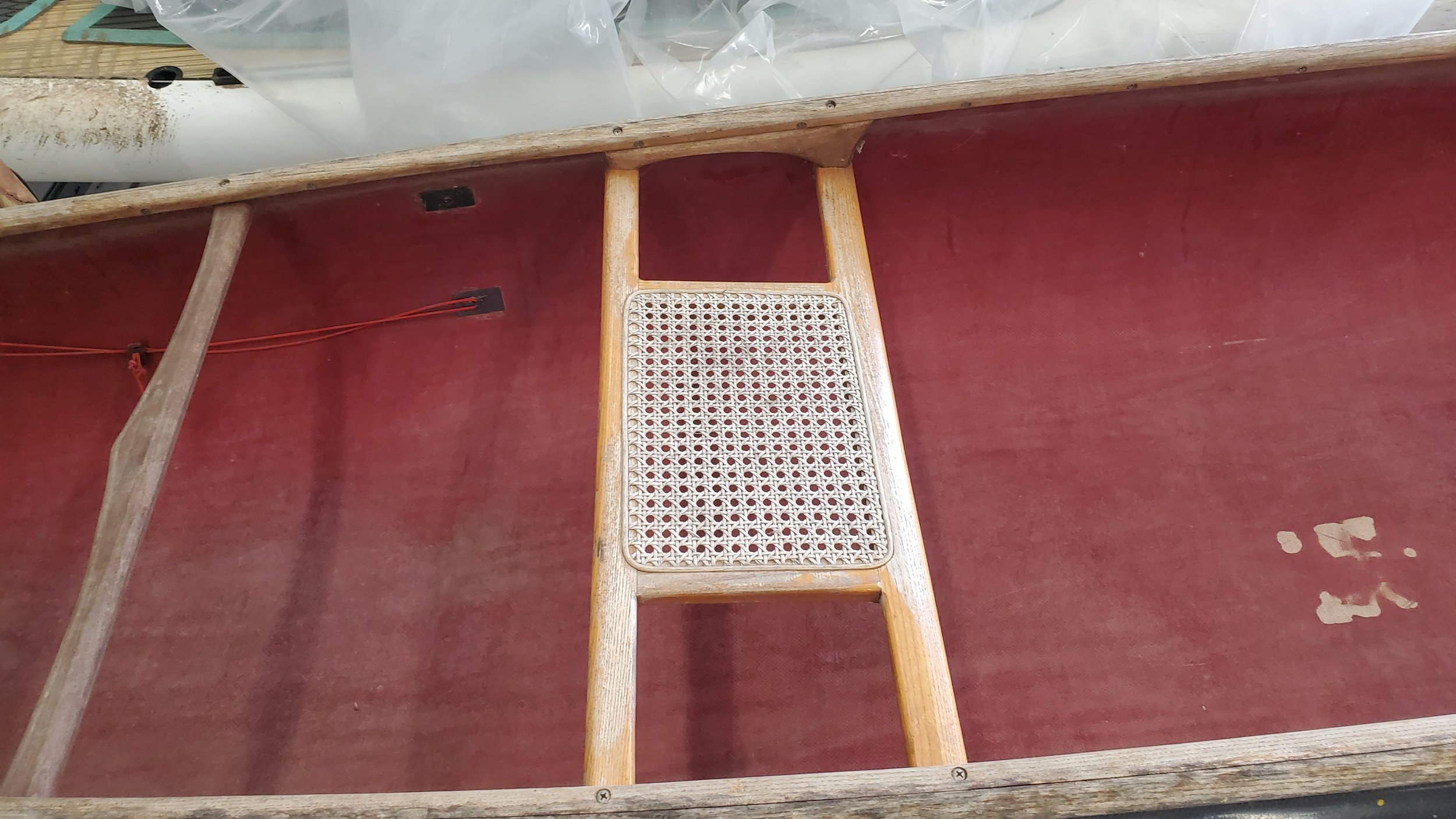
Request a Free Quote
Review the quote definitions and fill out the free quote request form below.
-
Essential Repair (cost-effective order)
Generally “essential-repair order” means we restore the craft to a standard of functionality that is acceptable under the conventional use of the item/watercraft. This includes reinforcing breaks, sealing cracks and dings, replacing rotten or worn out parts such as gunwales, seats and other trim pieces.
We strive to create clean repairs that maintain an acceptable aesthetic but they often reveal that a repair was indeed made. It’s common for a repair area to be the strongest part of your craft once it leaves our shop. If you are the type of person that cares only for function then a repair order is all that you require.
Example: I want the hole fixed in my canoe hull but I don’t care if you hide the repair with a matched gelcoat.
Refurbished Repair (most common order)
This is an essential repair that attempts to hide all signs that a repair was made. This is our most common request and no one does it better than NPS.
-
A “recondition order” is not necessarily a repair but can be added to a repair order or just a great way to breathe new life into your item/watercraft. Reconditioning includes cleaning, sanding, oiling, buffing/polishing, resin recoat, painting/gelcoating, for the purposes of looks and longevity. Basically like an oil change for your watercraft. A recondition order goes a long way to maintaining the quality of your boat or board for years to come.
Old boats are often greatly enhanced by a recondition alongside their repairs making them a viable option for daily use once more. Reconditioning also adds resale value if you want to make your item more attractive to potential buyers.
-
“Restoration order” is a much more rare project and the lead times are generally in excess of one calendar year. However, for the customer that wishes to make their watercraft like-new again, a restoration order is the only way to go.
For the customer that wants their recent Craigslist or marketplace find or grandpa’s old wood and canvas canoe restored to original glory, you need to look no further. Restoration projects include Kevlar/Carbon Composite, Wood, Fiberglass, Wood and Canvas, and more.
-
A “modification order” applies to any aftermarket alteration made to your item/watercraft that the owner is otherwise lacking confidence in a DIY approach. We get it. It can be intimidating to drill holes in something worth hundreds or thousands of your hard-earned dollars, especially something that can be sunk by holes.
Common modifications include:
Accessory Installation
New Seats/Backrests
Sonar Installation
Gear Mounts
Foot Braces
Sail Rigs
Custom contrivances of your own design
-
Tooling refers to creating the pattern from which a mold can be made. Molding refers to fabricating a fiberglass mold from a pattern that can be used to produce multiple parts.
For all Tooling/Molding Orders, contact Eli directly.